How cobots in manufacturing are changing the factory floor
The factory floor of the future is collaborative. Gone are the days when giant industrial robots worked in isolation behind safety cages. Instead, a new generation of automation technology is emerging that is designed to work seamlessly and safely side by side with people.
These collaborative robots, or cobots, are transforming manufacturing by increasing productivity, improving safety, and driving innovation. Cobots are smaller, more flexible, and easier to program than their traditional counterparts, making them ideal for a wide range of tasks and production environments.
Main advantages of cobots in manufacturing
Cobots are transforming the manufacturing industry for several reasons. Their inherent flexibility makes them perfect for a dynamic production environment. Unlike traditional industrial robots, which are usually programmed to perform a specific task, cobots can be effortlessly reprogrammed and redeployed to handle different tasks or production volumes.
This adaptability is invaluable for manufacturers looking to optimize their processes, streamline operations and achieve greater efficiency. Partnering with a Automation system integrator can ensure seamless integration of cobots into your manufacturing environment, maximizing their potential.
Their agility also makes them well suited for companies that produce smaller batches or where changeovers occur frequently.
Safety: A fundamental principle
Cobots are inherently safe in their design. Features like force sensors and speed limits allow them to work right alongside human workers without the need for bulky cages. Not only does this save valuable floor space, but it also significantly reduces the risk of workplace accidents, creating a safer environment for everyone. They are ideal for taking on repetitive or ergonomically risky tasks that lead to worker injuries.
Increase productivity
Cobots provide manufacturers with a tireless workforce that can work non-stop, 24/7. Unlike human workers, they don’t need breaks or time off. This directly translates to increased production, faster turnaround times, and the ability to meet demanding customer deadlines. Cobots can be deployed to work alongside your existing human team, maximizing the performance of your existing equipment and employees.
Given their combination of flexibility, improved safety and increased productivity, it’s easy to see why cobots are seeing such rapid growth in manufacturing.
Ideal areas of application for cobots
Cobots in manufacturing are not a one-size-fits-all solution, but they excel in certain areas. Here are some of the tasks and environments where their implementation often offers significant benefits:
Recurring tasks
Assembly work, machine operation, packaging, palletizing… these tasks are often characterized by repetitive movements that can lead to worker fatigue, errors and injuries. Cobots never get bored and perform these types of tasks flawlessly hour after hour, freeing up your human workforce to focus on more complex tasks, quality control and activities that require creativity and problem-solving skills.
Dangerous environments
Whether it’s extreme temperatures, hazardous chemicals, confined spaces, or heavy lifting, some manufacturing tasks simply pose risks for human workers. Cobots can take on these dangerous tasks, minimizing risk and creating a safer workplace overall.
Labor shortage
An increasingly common challenge for manufacturers is finding and retaining reliable workers, especially for repetitive or undesirable tasks. Cobots in manufacturing help fill these gaps by working tirelessly in situations where staffing can be challenging. This could involve night shifts, difficult working conditions, or simply tasks that human workers prefer to avoid.
Cobots offer a practical solution to these diverse manufacturing challenges. By strategically deploying cobots for specific, well-suited tasks, you can create a more productive and safer work environment.
Addressing common concerns about cobots
While the benefits of cobots in manufacturing are compelling, some have legitimate questions or reservations about this technology. It is helpful to address these concerns directly:
Job loss
The fear that cobots will eliminate human jobs is understandable, but it is important to remember that automation often leads to new tasks and opportunities. Cobots are ideal for taking over repetitive and physically demanding tasks and freeing up human workers for higher-value work such as programming, maintenance, analysis and quality control.
To ensure that cobot implementation results in a net gain for your team, it is important to upskill your current workforce for these evolving roles.
Cost
While cobots represent an investment, it’s important to consider the long-term return on investment (ROI). Factors such as lower labor costs, increased productivity, fewer workplace accidents, and improved efficiency add up to a payback period that can justify the initial outlay. In addition, the cost of cobots has been steadily decreasing, making them increasingly affordable for small and medium-sized manufacturers.
Companies that use cobots in manufacturing understand that this is not about replacing humans with machines, but rather about using these tools strategically to improve efficiency and create a more sustainable manufacturing operation.
Getting started with cobots
Harnessing the power of cobots in manufacturing requires careful planning and consideration to ensure a successful implementation.
Evaluate your needs
Start by analyzing your production processes to find out where cobots could have the biggest impact. Look for tasks that are repetitive, dangerous, have frequent quality issues, or where staffing is a constant challenge. A thorough needs analysis will ensure you invest in a cobot solution that directly addresses your most pressing problems.
Selecting an integrator
Cobot solutions are rarely “off the shelf.” Working with an experienced robotics integrator can simplify the selection, deployment and ongoing maintenance of your cobot system. A good integrator will help you select the right cobot hardware and design a system tailored to your specific work environment.
You also provide basic training to your team to ensure employees can work smoothly and productively with their new automated colleagues.
By following these steps and working with the right experts, you can unlock the true potential of cobots in your manufacturing operation. It’s a transformative step forward that increases efficiency and safety.
The future is collaborative
Cobots in manufacturing are not just a trend. They represent the future of modern manufacturing. Manufacturers who use this technology will succeed in an increasingly competitive and dynamic market.
The benefits are obvious: improved productivity through continuous, consistent operation and the ability to automate repetitive tasks; increased safety by reducing worker exposure and ergonomically risky activities; and the flexibility to adapt to changing production requirements, new product lines or fluctuating customer demands.
Cobots are a powerful tool to create a smarter factory floor, where humans and machines work seamlessly together to achieve new levels of efficiency and innovation. If you’re ready to create a smarter, safer, and more efficient factory, it’s time to explore the world of cobots and find out how they can help you navigate the uncharted territory of the future manufacturing landscape.
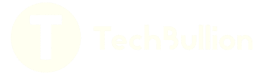